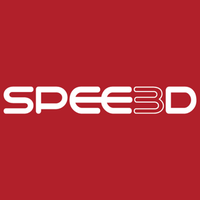
SPEE3D
@officialspee3d
Ultra fast and cost effective, SPEE3D's LightSPEE3D and large format WarpSPEE3D and XSPEE3D printers manufacture industrial grade metal parts in minutes.
ID: 918702168642764801
http://www.spee3d.com 13-10-2017 04:57:20
1,1K Tweet
695 Followers
160 Following
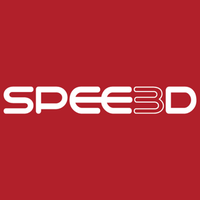
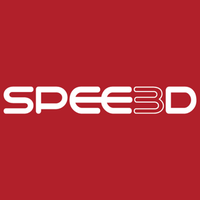
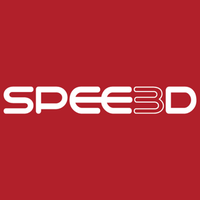
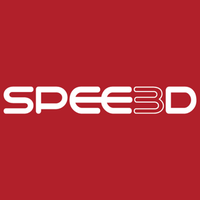
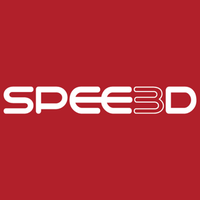
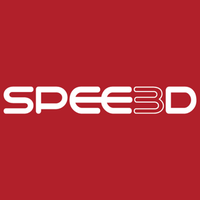
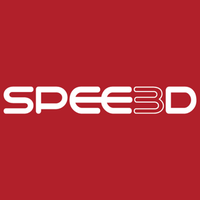
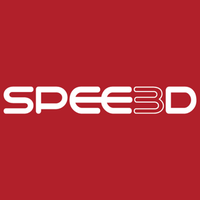
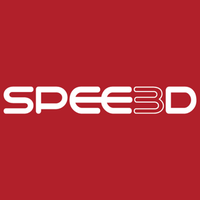
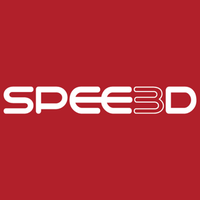
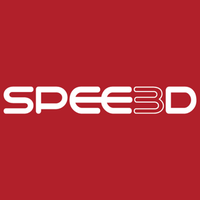
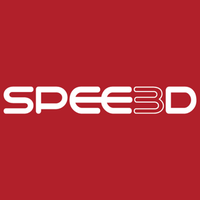
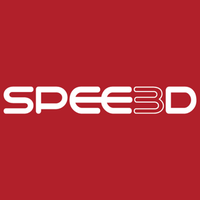
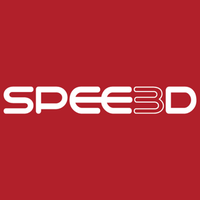
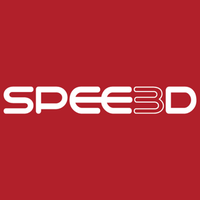
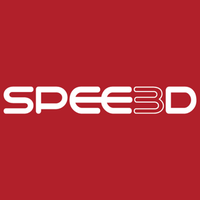
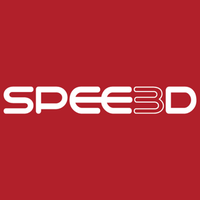
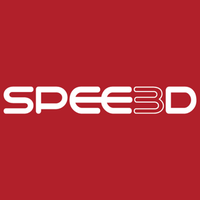
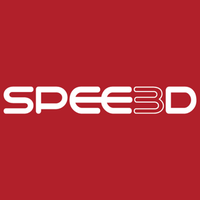
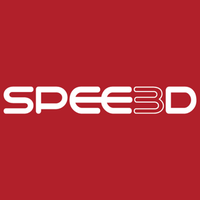